Aluminum alloy die casting is a manufacturing process that uses molten aluminum to create complex, high-precision parts. The molten aluminum is injected under pressure into a die cavity, which gives the part its final shape.
The two main types of die casting are HPDC and LPDC. HPDC is a more demanding process than LPDC, and the materials used must be able to withstand the higher pressures and temperatures involved.
Materials used in HPDC
HPDC alloys typically have a higher silicon content than LPDC alloys, which improves their fluidity and castability. HPDC alloys also typically have a lower magnesium content than LPDC alloys, which reduces the risk of shrinkage porosity.
Some common HPDC alloys include:
A380
A384
A390
Materials used in LPDC
LPDC alloys typically have a lower silicon content than HPDC alloys, which reduces their fluidity and castability. However, they also have a higher magnesium content, which improves their ductility and toughness.
Some common LPDC alloys include:
A360
A413
A443
View More Aluminum Alloy
Aluminum Alloy |
Properties |
Applications |
A380 |
Excellent fluidity, pressure tightness, and resistance to hot cracking |
Housings and components in automotive, electronics, and consumer goods |
A383 |
Improved corrosion resistance and heat resistance compared to A380 |
Components requiring better thermal performance, such as heat sinks and electronic enclosures |
A360 |
Good corrosion resistance and high strength at elevated temperatures |
Components exposed to high temperatures, such as automotive transmission cases |
ADC12 |
High strength, excellent corrosion resistance, and good casting characteristics |
Automotive components, electrical housings, and various consumer goods |
AlSi12 |
Aluminum-silicon alloy with good fluidity and castability |
Electronic components, communications equipment, and lightweight structural parts |
AlSi9Cu3 |
Good combination of strength, castability, and corrosion resistance |
Components in automotive applications, including engine parts and structural elements |
AlSi10Mg |
Good strength, corrosion resistance, and high thermal conductivity |
Components requiring high strength-to-weight ratios, such as aerospace and automotive parts |
EN AC-43400 |
Good mechanical properties, including high hardness and strength |
Applications where higher hardness and wear resistance are required, such as gears and other mechanical components |
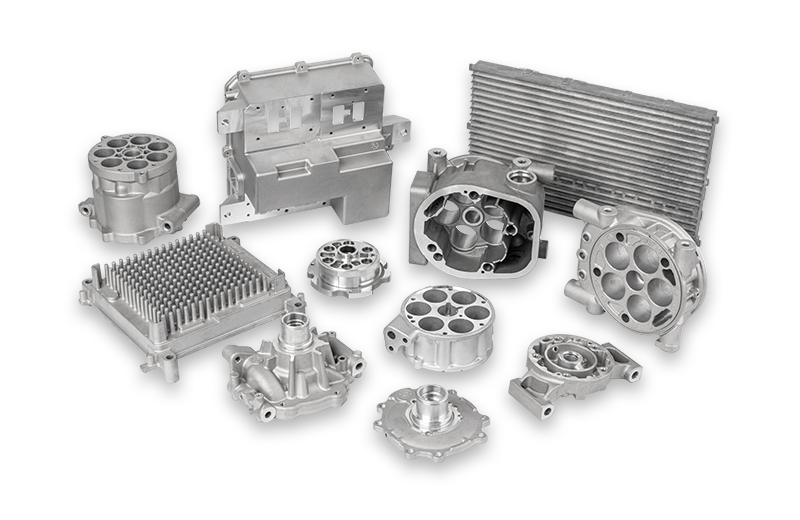
Choosing the right material
The choice of alloy for a particular die casting part will depend on the specific requirements of the application. Factors to consider include:
The strength required
The ductility required
The corrosion resistance required
The complexity of the part
The thickness of the part walls
The die casting process being used
HPDC vs. LPDC
HPDC alloys are generally better suited for parts that require high strength, good dimensional accuracy, and a smooth surface finish. LPDC alloys are generally better suited for parts that are complex in shape or have thick walls.
Here is a table comparing HPDC and LPDC alloys:
Property |
HPDC alloy |
LPDC alloy |
Silicon content |
Higher |
Lower |
Magnesium content |
Lower |
Higher |
Fluidity |
Better |
Worse |
Castability |
Better |
Worse |
Shrinkage porosity |
Lower risk |
Higher risk |
Strength |
Higher |
Lower |
Ductility |
Lower |
Higher |
Corrosion resistance |
Good |
Good |
Complexity of parts |
Suitable for complex parts |
Suitable for complex parts |
Thickness of part walls |
Suitable for thin walls |
Suitable for thick walls |
Die casting process |
HPDC |
LPDC |