The quality of
aluminum high pressure die-casting cylinder front covers is influenced by a variety of factors that interact throughout the manufacturing process. One critical factor is the quality of the aluminum alloy used. The choice of alloy and its composition directly affects the flow characteristics, solidification behavior, and mechanical properties of the casting. High-quality alloys with precise compositions are essential for achieving consistent and defect-free results.
Equally important is the design and maintenance of the dies used in the casting process. The die design, including the gating system, runner layout, and cooling channels, must be carefully engineered to ensure proper filling of the mold cavity and uniform cooling of the casting. Regular maintenance of the dies is crucial to prevent wear and ensure dimensional accuracy and surface finish.
Control over casting parameters such as metal temperature, injection pressure, and cooling rate is essential for producing high-quality cylinder front covers. Optimal parameter settings are determined through experimentation and process optimization to achieve the desired casting properties while minimizing defects such as porosity, shrinkage, and surface irregularities.
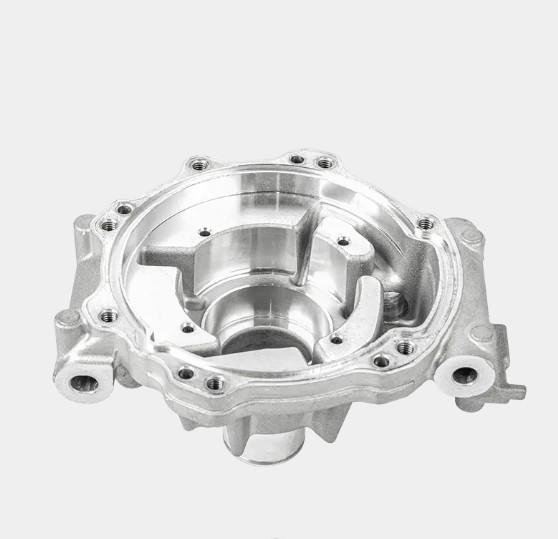
Effective mold release agents and lubricants are used to facilitate the ejection of the casting from the die and prevent sticking. Proper application of release agents and lubricants helps ensure smooth ejection and minimizes the risk of surface defects.
Process monitoring and control systems play a vital role in maintaining consistent quality throughout the die-casting operation. Advanced monitoring techniques allow operators to track key process variables in real-time and make adjustments as needed to ensure that casting quality meets specifications.
Post-casting machining and finishing operations are also critical for achieving the desired final product quality. Machining techniques such as trimming and deburring remove excess material and refine dimensional accuracy, while surface finishing processes such as polishing or coating enhance aesthetics and corrosion resistance.
Quality assurance measures, including comprehensive testing protocols and non-destructive inspection techniques, are employed to verify the integrity of the castings and ensure compliance with customer requirements and industry standards. This includes testing for dimensional accuracy, mechanical properties, and surface finish.